1 Global Metal Shims Market Insight Analysis
The global Metal Shims market value is expected to reach USD 203.6 Million in 2025, with a CAGR of 3.93% during 2025-2033.
Shims are thin and often tapered or wedge-shaped materials used to fill small gaps or spaces between objects. Shims are usually used to support, adjust to better fit or provide a level surface. Shims can also be used as gaskets to fill gaps between wear-prone parts. Many materials can be used to make Shims, such as metal, stone, wood, plastic, paper, etc. Among them, the most widely used is the Metal Shims.
Figure Global Metal Shims Market Size (M USD) and CAGR (2025-2033)
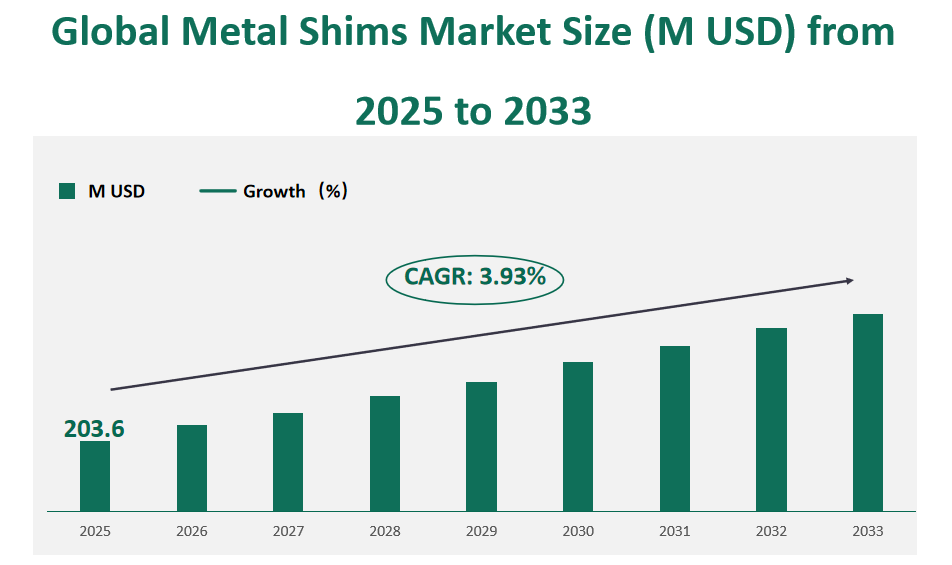
2 Metal Shims Market Growth Drivers and Restraints
Demand expansion in downstream industries
Metal gaskets are widely used in mechanical engineering and automotive engineering, and the continued development of these two industries is the core driving force.
Mechanical engineering: The popularization of industrial equipment manufacturing and automated machinery has increased the demand for high-precision gaskets for equipment support, sealing and gap adjustment. For example, the upgrading of manufacturing industry has driven the growth of demand for corrosion-resistant and high-strength metal gaskets.
Automotive engineering: The growth of automobile production and the development of new energy vehicle technology (such as the precision assembly of motors and battery components) have driven the demand for gaskets, especially the increase in the use of lightweight aluminum alloy and stainless steel gaskets.
Industrialization process in emerging markets
Industrialization and urbanization in emerging economies such as China, India, and Brazil have driven the expansion of manufacturing. For example, China’s “14th Five-Year Plan” supports high-end equipment manufacturing and India’s automobile industry localization policy has stimulated the local production and procurement demand for metal gaskets.
Material technology and performance upgrades
Advances in metal material technology (such as the research and development of high-strength stainless steel and corrosion-resistant brass) have improved the applicability of gaskets. For example, stainless steel gaskets have excellent corrosion resistance, and their application in harsh environments such as chemical and medical applications continues to rise (53.56% market share in 2020).
Policy and environmental protection requirements
Global environmental regulations are becoming stricter, driving metal gaskets to replace plastic gaskets (such as the EU RoHS directive restricting the use of plastics). The recyclability and durability of metal materials make them more in line with sustainable development needs. In addition, countries’ strict standards for industrial equipment leakage control (such as US EPA regulations) have increased the purchase volume of high-performance metal gaskets.
Supply chain regionalization trend
Under the trend of supply chain diversification after the epidemic, companies tend to establish more stable supply chains in the region. For example, North American and European companies have increased their investment in local production and reduced their dependence on Asian supply chains, driving regional market growth.
Raw material price fluctuations
The prices of the main raw materials for metal gaskets (such as steel, aluminum, and copper) are significantly affected by the global commodity market. For example, the rise in iron ore prices in 2021 led to an increase in the cost of carbon steel gaskets by about 8%, and stainless steel gaskets experienced price instability due to fluctuations in nickel prices. Raw material costs account for 72.37% of production costs, and price fluctuations directly squeeze corporate profit margins.
Substitute product competition
Plastic gaskets and composite gaskets replace metal gaskets in low-load, non-precision scenarios. For example, polyethylene gaskets cost 30%-50% less than aluminum gaskets, and compete with metal gaskets in the field of general machinery. Especially in emerging markets, the popularity of low-cost alternative materials has slowed the market penetration of metal gaskets.
Rising labor costs
Labor costs in developed countries continue to rise (for example, the average monthly salary in the US manufacturing industry increased from US$4,987 in 2016 to US$5,486 in 2019), pushing up production costs. Companies with insufficient automation are under pressure, while the labor advantages of emerging markets are gradually offset by industrial transfer.
Market competition is fragmented and low in concentration
The global metal gasket market is fragmented, with the top three companies accounting for only 19.24% of the market share (2020), and the large number of small and medium-sized enterprises has led to fierce price competition. For example, companies such as Matenaer Corporation and AccuTrex Products in the United States have been involved in price wars for a long time, compressing the industry’s profit level.
Technical barriers and insufficient R&D investment
High-end metal gaskets (such as precision gaskets for aerospace) require high-precision processing technology (such as laser cutting and water jet processing), but small and medium-sized enterprises have limited R&D investment and find it difficult to break through technical barriers. For example, leading companies such as SKF monopolize the high-end market through patent layout (such as precision alignment gasket technology), while small and medium-sized enterprises can only focus on the mid- and low-end fields.
3 Technological Innovations in the Metal Shims Market
Material innovation
Lightweight materials: Aluminum alloy gaskets have replaced traditional steel in the automotive and aviation fields due to their low density and easy processing. In 2020, the market share reached 3.56%, and the annual compound growth rate reached 4.22%.
Composite metal technology: Coating technology (such as nickel plating and zinc plating) improves the corrosion resistance of carbon steel gaskets, extends service life, and reduces maintenance costs.
Manufacturing process upgrade
Digital production: Leading companies introduce CAD design, CNC machining (CNC) and automated production lines to improve precision and efficiency. For example, Aloma Shims uses laser cutting technology to control the gasket tolerance within ±0.001 inches.
3D printing technology: Some companies try to produce complex structure gaskets through metal 3D printing to reduce material waste and shorten customized production cycles, which is suitable for high-end fields such as aerospace.
Product intelligence and standardization
Smart gaskets: Smart gaskets with integrated sensors (such as SPM Instrument’s vibration monitoring gaskets) can monitor the operating status of equipment in real time, predict maintenance needs, and promote the transformation of products to services.
Unification of industry standards: International standard organizations (such as ISO) promote the standardization of gasket specifications, reduce customer customization costs, and promote cross-regional sales.
Horizontal mergers and acquisitions to expand market share
Heading companies integrate resources through mergers and acquisitions to expand product lines and regional layouts. For example:
SKF: By acquiring a precision gasket manufacturer in the United States, it has increased its penetration in the North American automotive market. In 2020, its market share reached 8.14%, ranking first in the world.
Matenaer Corporation: Acquired competitor Bokers, Inc., integrated brass gasket production lines, and enhanced its competitiveness in the field of mechanical engineering.
Vertical integration optimizes the supply chain
Companies acquire raw material suppliers upstream or expand distribution channels downstream to control costs and improve response speed. For example:
AccuTrex Products: Invest in aluminum profile processing plants to ensure a stable supply of raw materials and cope with aluminum price fluctuations.
Aloma Shims: Establish a global distribution network, directly reach small and medium-sized customers through e-commerce platforms, and shorten sales cycles.
Emerging market layout
Multinational companies enter emerging markets by acquiring local companies. For example:
European Seeger-Orbis acquires a local gasket manufacturer in India, using its low-cost production base to radiate the South Asian market and circumvent tariff barriers.
Chinese companies reduce export costs by acquiring Southeast Asian processing plants to cope with the tariff pressure brought about by Sino-US trade frictions.
Technology-based mergers and acquisitions strengthen R&D
Companies acquire technology-based start-ups to obtain patents and talents. For example:
SPIROL: Acquires a technology company focusing on metal composite materials to accelerate the development of corrosion-resistant gaskets and consolidate its advantages in the chemical industry.
Stephens Gaskets Ltd: Acquires a laser processing company to improve the production capacity of precision gaskets and enter the high-end equipment market.
4 Global Metal Shims Market Size by Type
Stainless Steel Shims are expected to hold the largest market share in 2025, with a projected revenue of 109.32 million USD. Stainless steel shims are highly valued for their corrosion resistance, durability, and ability to withstand extreme temperatures and pressures. These properties make them ideal for use in mechanical engineering and automotive applications where reliability and longevity are critical. Stainless steel shims are commonly used in engine components, gaskets, and other parts that require high precision and resistance to wear and tear.
Carbon Steel Shims are projected to generate a revenue of 12.49 million USD in 2025. Carbon steel shims are known for their cost-effectiveness and strength. They are widely used in applications where high strength and durability are required but where the risk of corrosion is minimal. Carbon steel shims are commonly found in mechanical engineering applications, such as in the construction of heavy machinery and industrial equipment. Their affordability and ease of manufacturing make them a popular choice for many industries.
Brass Shims are expected to contribute 62.06 million USD to the market revenue in 2025. Brass shims are valued for their excellent conductivity, both thermal and electrical, as well as their resistance to corrosion. These properties make them suitable for applications in electrical and mechanical engineering. Brass shims are often used in environments where sparking must be avoided, such as in explosive atmospheres. Their ability to resist tarnishing also makes them ideal for use in food processing and medical equipment.
Aluminum Shims are projected to generate a revenue of 7.20 million USD in 2025. Aluminum shims are lightweight and highly resistant to corrosion, making them ideal for applications where weight is a critical factor. They are commonly used in the automotive industry, particularly in engine components and other parts where reducing weight can improve fuel efficiency. Aluminum shims are also used in the food and beverage industry due to their non-reactive nature and ease of recycling.
Table Global Metal Shims Market Size by Type in 2025
Type | Market Size (M USD) 2025 |
---|---|
Carbon Steel Shims | 12.49 |
Brass Shims | 62.06 |
Aluminum Shims | 7.20 |
Stainless Steel Shims | 109.32 |
Others | 12.53 |
5 Global Metal Shims Market Size by Application
Mechanical Engineering: The market revenue is expected to be 94.86 million USD. This significant figure reflects the crucial role of metal shims in industrial equipment manufacturing, automation machinery, and other aspects within mechanical engineering. High – precision and high – performance metal shims are in great demand to ensure the proper operation and assembly of mechanical equipment.
Automotive Engineering: The market revenue is projected to be 69.59 million USD. With the continuous development of the automotive industry, especially the rise of new energy vehicles, metal shims are essential for components such as motors and batteries. The demand for lightweight and durable metal shims in automotive engineering is steadily increasing.
Table Global Metal Shims Market Size by Application in 2025
Application | Market Size (M USD) 2025 |
---|---|
Mechanical Engineering | 94.86 |
Automotive Engineering | 69.59 |
Others | 39.15 |
6 Global Metal Shims Market Size by Region
North America is anticipated to be a dominant player in the global Metal Shims market, with a projected market size of 78.67 million USD in 2025. This region has consistently shown a strong inclination towards technological advancements and industrial automation, which drives the demand for precision components like Metal Shims. The growth in North America can be attributed to the presence of well-established manufacturing sectors and a robust economy that supports high-value industrial production. Additionally, the region’s focus on research and development within the automotive and aerospace industries further propels the demand for Metal Shims.
Europe is projected to hold a substantial share of the global Metal Shims market, reaching a market size of 54.73 million USD in 2025. The European market is characterized by stringent environmental regulations and a push towards sustainable manufacturing practices. This has led to an increased demand for Metal Shims in applications that require durability and resistance to harsh conditions, such as in the automotive and renewable energy sectors. Moreover, Europe’s strong emphasis on industrial automation and machinery manufacturing supports a steady demand for Metal Shims. The region’s economic stability and the presence of several leading engineering and automotive companies contribute to its significant market share.
China is expected to emerge as a significant contributor to the global Metal Shims market, with a projected market size of 32.86 million USD in 2025. The rapid industrialization and urbanization in China have led to a surge in demand for Metal Shims across various sectors, including construction, automotive, and machinery manufacturing. The Chinese government’s initiatives to boost domestic manufacturing capabilities and its focus on high-speed rail and infrastructure development further drive the demand for Metal Shims. Additionally, China’s role as a global manufacturing hub supports the need for high-quality industrial components, positioning it as a key player in the Metal Shims market.
Figure Global Metal Shims Market Size (M USD) by Region in 2025
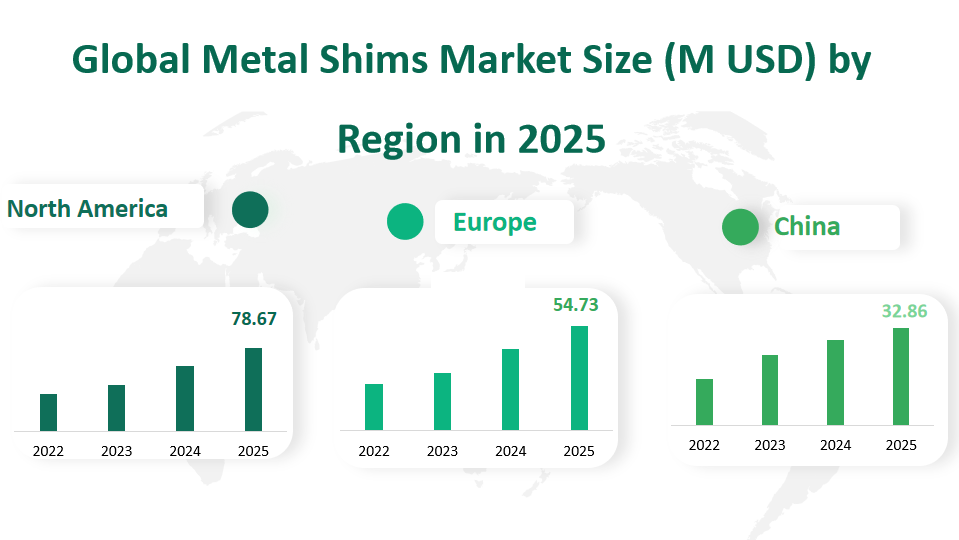
7 Global Metal Shims Market Analysis by Major Players
SKF
Company Profile: SKF, established in 1907, is a renowned Swedish company specializing in the manufacturing of bearings, seal rings, mechatronics, maintenance, and lubrication products, services, and solutions. With a global presence, SKF operates numerous plants across Europe, America, and Asia, serving customers worldwide.
Business Overview: SKF stands as a leader in providing sustainable solutions and services to a variety of industries. Their business model revolves around enhancing reliability, efficiency, and environmental performance of machinery and processes. By focusing on innovation and quality, SKF aims to create value for customers while contributing to a sustainable future.
Product Offered: SKF offers a diverse range of Metal Shims, including high-quality stainless steel shims designed for accurate vertical machinery alignment. Their shims are known for being reusable, easy to fit and remove, and having close tolerances for precise alignment. SKF’s product line also includes shim kits that are made of stainless steel, allowing for accurate machine adjustment and are marked with thickness for convenience.
Matenaer Corporation
Company Profile: Founded in 1972, Matenaer Corporation is a prominent player in the Metal Shims industry, primarily based in the USA with a sales reach mainly in America. The company has built a strong reputation for producing special washers and metal stampings for various industries.
Business Overview: Matenaer Corporation caters to fastener distributors and original equipment manufacturers, providing parts for industries like agriculture, automotive, construction hardware, and consumer goods. They focus on manufacturing close-tolerance and hard-to-make washers, showcasing their expertise in custom solutions and specialized technologies such as electroplating and coating.
Product Offered: Matenaer specializes in producing washers from materials like mild steel, stainless steel, brass, and aluminum. They offer shims that can be customized according to customer requirements, including a variety of special technologies. Their Metal Shims are designed to meet the specific needs of different machinery and equipment, ensuring a perfect fit and function.
AccuTrex Products, Inc.
Company Profile: AccuTrex Products, Inc., established in 1980, is a manufacturer of custom shims, gaskets, metal stampings, sheet metal fabrication, and assemblies. They operate primarily in the USA with a global sales reach, accommodating customers’ precise needs across various production scales.
Business Overview: AccuTrex Products, Inc. is committed to delivering custom metal components and shims that meet the stringent requirements of their clients. They offer a range of services including sheet metal fabrications, metal stampings, EDM machining, laser cutting, and tube bending. Their headquarters and Precision Parts Division provide comprehensive manufacturing solutions to ensure customer satisfaction.
Product Offered: AccuTrex offers a variety of Metal Shims, including custom brass and carbon steel shims. They utilize advanced laser and abrasive waterjet cutting technologies to produce shims that are resistant to corrosion, wear, and tear while offering thermal and electrical conductivity. Their products are designed to eliminate tooling and related expenses, ensuring a cost-effective solution for their clients.